Cutting a hole in a stainless steel sink is often necessary for installing fixtures such as faucets, soap dispensers, or water filtration systems. Understanding how to cut a hole in a stainless steel sink is crucial for achieving a professional and functional outcome.
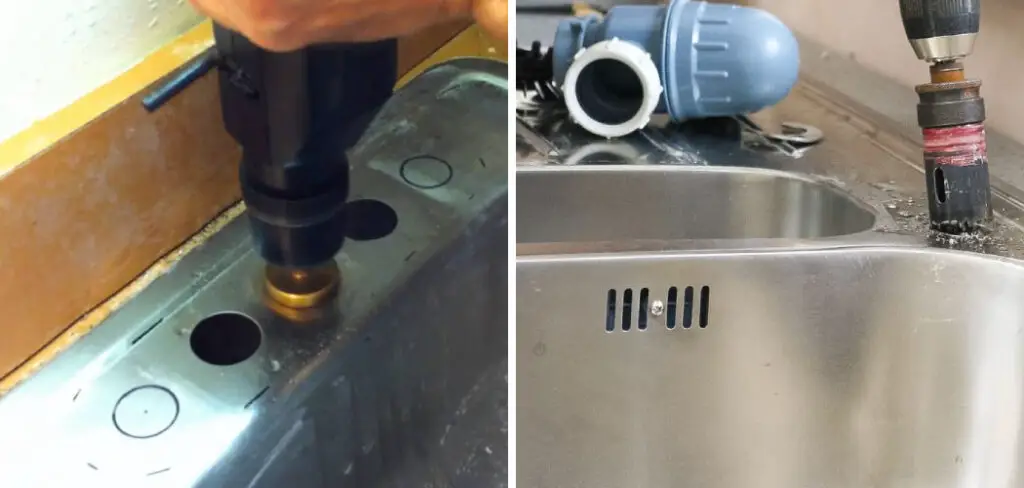
Precise measurements and careful execution are paramount to ensure that the fixture fits perfectly and the integrity of the sink is maintained. Missteps can lead to misalignments, leaks, or even damaging the sink.
To successfully cut a hole, you’ll need several specialized tools and to follow a structured process. These tools typically include a drill, jigsaw or hole saw, cutting oil, masking tape, and sandpaper.
The process involves preparing the sink, securing it in place, drilling starter holes, cutting the desired hole, and deburring and smoothing the edges. Each step requires patience and attention to detail to ensure a smooth and precise cut.
Safety Precautions
When learning how to cut a hole in a stainless steel sink, safety is of utmost importance. Wearing safety goggles and gloves is crucial to protect your eyes from metal shavings and your hands from sharp edges during cutting. If you’re using power tools such as a drill or jigsaw, ear protection should also be worn to shield your ears from high noise levels.
Ensuring the sink and surrounding area are stable is another key safety measure. Use clamps or a stable support system to secure the sink and prevent any unexpected movement while cutting.
Additionally, clear the area around the sink to avoid any tripping hazards and ensure easy access to your tools. Following these precautions helps protect you from injury and ensures a smoother, more precise cutting process.
Materials and Tools Needed
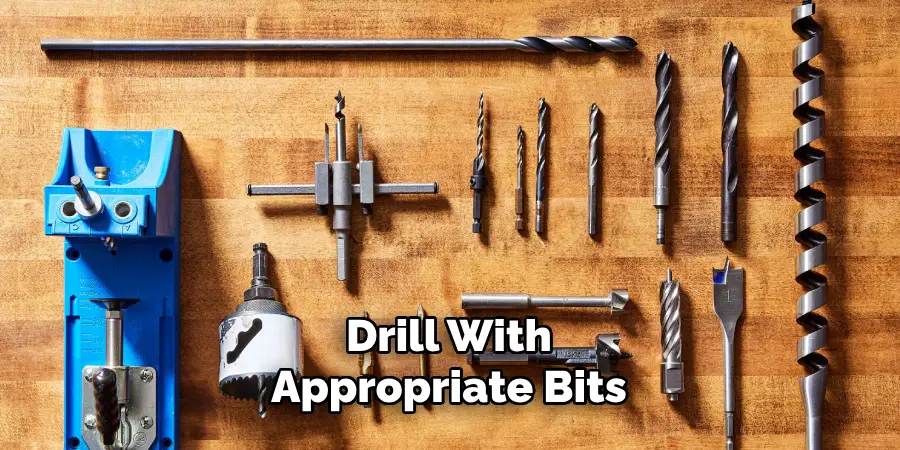
To effectively learn how to cut a hole in a stainless steel sink, you’ll need a specific set of materials and tools. Begin with a template or marking tool to outline the exact location and size of the hole. Next, a drill with appropriate bits is essential for creating starter holes; high-speed steel (HSS) or cobalt bits are ideal for stainless steel. You’ll also require a jigsaw or hole saw with metal-cutting blades to make the main cut. Masking tape is useful for preventing scratches on the sink’s surface and keeping the marked line visible. Applying lubricant or cutting oil will reduce friction and prevent overheating, ensuring a smoother cut.
Using the correct tools is crucial because stainless steel is a tough and resilient material. Incorrect tools can lead to damage or imprecise cuts, compromising the sink’s functionality and appearance.
Optionally, you might consider a file or deburring tool for smoothing out any rough edges left after the cut. These tools help in removing any burrs, ensuring a clean and polished edge which reduces the risk of injury and provides a professional finish. Finally, having sandpaper on hand can further smooth the cut edges and refine the overall finish.
How to Cut a Hole in A Stainless Steel Sink: Cutting Process
01.Prepare the Sink
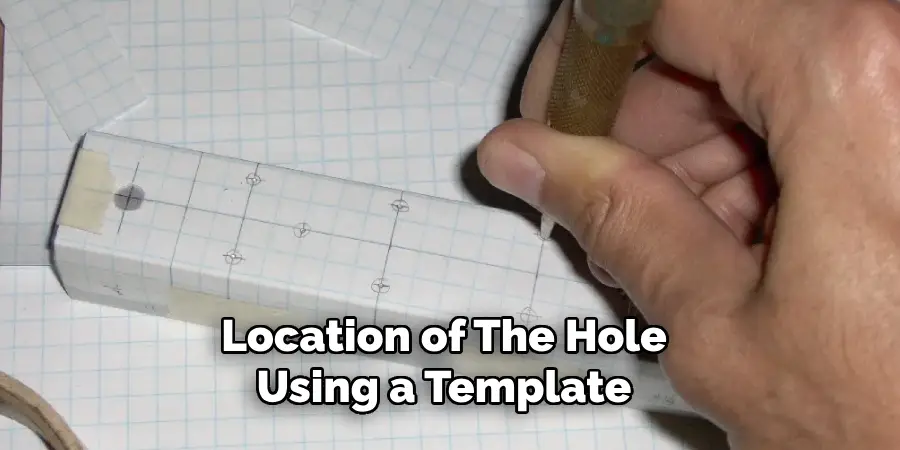
Before starting the cutting process, it’s crucial to prepare the sink. Begin by emptying the sink and cleaning the area where the hole will be cut.
This ensures that there is no debris or residue that could interfere with the cutting. Next, measure and mark the exact location of the hole using a template or marking tool.
Accurate measurements are essential to ensure the fixture fits perfectly and functions correctly. Double-check your measurements and markings to ensure precision. Proper preparation sets the foundation for a smooth and successful cutting process.
02.Secure the Sink
Securing the sink is a vital step before you start drilling or cutting. Use clamps or a stable support system to hold the sink firmly in place, ensuring it doesn’t move during the process. This stability is essential for making accurate cuts and preventing unexpected slippage that could result in mistakes or injuries.
Additionally, make sure the area around the cutting site is clear and accessible. Remove any obstructions to ensure you have enough space to maneuver your tools comfortably. A well-secured sink contributes significantly to the safety and precision of the cutting process.
03.Drill Starter Holes
Creating starter holes is a crucial step in the cutting process. Use a drill with a small bit, preferably a high-speed steel (HSS) or cobalt bit, to make starter holes around the marked circle at key points.
These holes serve as guide points for your cutting tool, ensuring you follow the marked outline accurately and providing entry points for the jigsaw or hole saw.
Begin by drilling slowly to prevent the bit from skidding off the smooth surface. Increase the speed gradually as the bit starts penetrating the metal. Space the starter holes evenly around the circle to make the cutting process smoother and more manageable.
These starter holes also help reduce the risk of the cutting tool slipping, which could lead to uneven edges or potential injury.
04.Cutting with a Jigsaw or Hole Saw
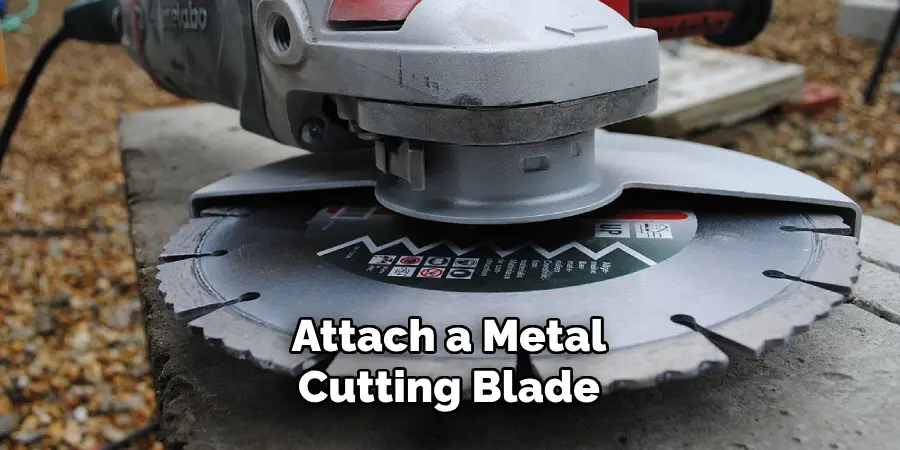
Once the starter holes are drilled, you can begin the main cutting process using a jigsaw or hole saw. Attach a metal-cutting blade to your chosen tool, ensuring it is the appropriate type for stainless steel. If you’re using a hole or saw, make sure it’s designed for metalwork.
Start cutting by carefully inserting the blade into one of the starter holes, following the marked circle.
Apply steady, even pressure to guide the tool along the marked path without forcing it, which could result in uneven cuts or damage to the blade. If using a jigsaw, keep a firm grip and move slowly to allow the blade to cut, reducing the risk of the blade slipping or getting damaged.
Continuously check your progress to ensure you are precisely cutting along the marked line. Taking your time and working carefully will yield the best results, ensuring the hole is clean and accurately positioned.
05.Use Cutting Oil or Lubricant
It’s important to apply cutting oil or a suitable lubricant to the cutting area during the cutting process.
This reduces friction and heat buildup, which can dull the cutting tool and cause it to lose efficiency. Apply the lubricant generously before you start cutting and reapply as necessary to keep the tool working smoothly.
Cutting oil helps maintain the sharpness of the blade and prevents overheating, which could warp the metal or damage the tool. Proper lubrication ensures a cleaner cut and prolongs the lifespan of your tools, contributing to a higher-quality finish.
06.Deburring and Smoothing
After successfully cutting the hole, the next step is to deburr and smooth the edges. This is essential to remove any rough edges or burrs that could cause injury or interfere with the installation of the fixture.
Use a file or a deburring tool to smooth the edges around the hole. Slowly work your way around the entire circumference, ensuring that all sharp edges are adequately filed down. Pay particular attention to any areas where the metal appears jagged or uneven.
Once the major burrs are removed, you can use finer sandpaper to further smooth the edges, providing a clean and polished finish.
This not only improves safety by minimizing the risk of cuts but also ensures that the fixture will fit snugly and securely in the hole, providing a professional appearance.
07.Final Touches
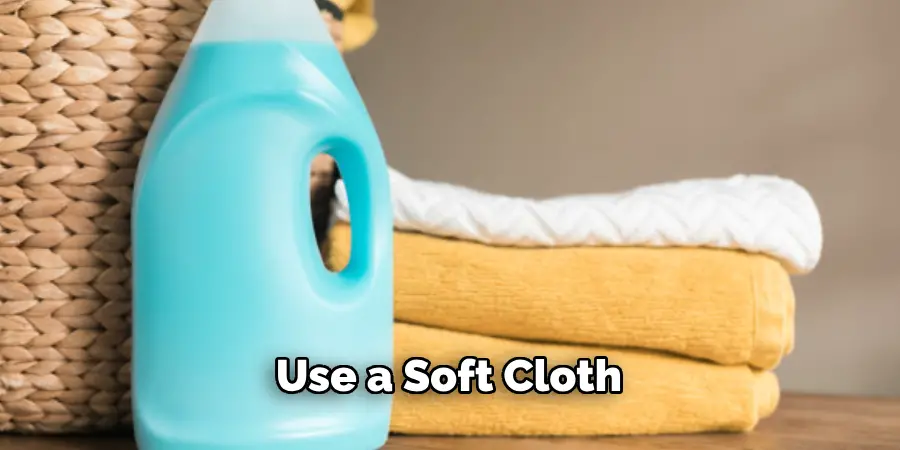
The final step involves cleaning the sink thoroughly to remove any metal shavings or debris resulting from the cutting process.
Use a soft cloth and a mild cleaner to wipe down the entire area, removing all particles. Inspect the hole to verify that it is smooth and has the correct dimensions for the fixture you intend to install.
A meticulous inspection at this stage can prevent future installation issues. Once the area is clean and the hole meets your specifications, you are ready to install the fixture, confident that the sink has been properly prepared and cut.
Proper Cleanup and Maintenance
Dispose of any metal shavings or debris safely to avoid potential injury. Use a brush, dustpan, or vacuum designed for metal particles to ensure a thorough cleanup.
Afterward, clean and store your tools properly to maintain their longevity; wipe them down with a cloth and apply a light coat of oil to prevent rust. Lastly, regularly inspect the sink, particularly around the cut area, to prevent corrosion.
If necessary, apply a suitable protective coating to the cut edges and address any signs of rust immediately to ensure the sink remains functional and in good condition.
Conclusion
Cutting a hole in a stainless steel sink requires careful preparation, precision, and adherence to safety guidelines. The process begins with securing the sink and ensuring a stable work environment, followed by drilling starter holes to guide your cutting tool.
Using a jigsaw or hole saw, cut along the marked outline with steady pressure, applying cutting oil to reduce friction. After cutting, deburr and smooth the edges for a clean finish, then thoroughly clean the sink to remove metal shavings.
Patience and precision are crucial to achieving a professional result throughout the process. Understanding how to cut a hole in a stainless steel sink ensures not only a successful project but also the longevity of your sink.
Maintain the sink’s integrity by applying protective coatings to cut edges and promptly addressing any signs of rust. Regular inspection and proper cleanup will keep your sink in top condition for years to come.
Professional Focus
Angela Ervin, a former interior designer turned blogger, specializes in kitchen design and renovations. Through her website, she blends her passion for cooking with design expertise, sharing practical and creative ideas. Known for balancing functionality and beauty, Angela’s insightful content has made her a trusted voice in home design and lifestyle.
About the Author
Angela Ervin, an experienced interior designer and blogger, combines her passion for kitchen renovations with storytelling. Living in Petersburg with her family, she enjoys cooking and testing her projects firsthand. Known for her humor and relatable style, Angela shares creative, functional design insights through her content, making her a trusted voice in home design.
Education History
University: Virginia Commonwealth University
Degree: Bachelor of Fine Arts (BFA) in Interior Design
- Angela’s education at VCU focused on mastering core interior design principles, including spatial planning, color theory, materials selection, and sustainable design practices.
- She gained hands-on experience through studio projects and collaborative design exercises, which honed her ability to create functional and aesthetically pleasing environments.
- Her coursework also emphasized problem-solving and practical applications of design, preparing her for real-world projects like her self-directed kitchen renovations.
- The program’s strong foundation in both technical skills and creative expression shaped Angela’s ability to seamlessly integrate form and function in her work.